Many advanced technologies are changing our lives every day. The advent and growth of the Electric Vehicle (EV) is a major example of just how much those changes can mean for our business life — and for our personal lives.
Technological advances and environmental regulatory pressures on internal combustion engine (ICE) vehicles are driving the expanding interest in the EV market. Many established automobile manufacturers are introducing new EV models, alongside new start-ups entering the market. With the selection of makes and models available today, and many more to come, the possibility that we all may be driving EVs in the future is closer to reality than ever.
The technology that powers the EVs of today demands many changes from the way traditional vehicles have been manufactured. The process to build EVs requires nearly as much design consideration as the aesthetics of the vehicle itself. That includes a stationary line of robots specifically designed for EV applications — as well as flexible production lines with mobile robots that can be moved in and out at various points of the line as needed.
In this issue we will examine what changes are needed to efficiently design and manufacture EVs today. We will talk about how processes and production procedures differ from those used to manufacture gas-powered vehicles.
Design, components and manufacturing processes
Although the development of the EV was vigorously pursued by researchers and manufacturers in the early twentieth century, interest was stalled due to cheaper cost, mass-produced gasoline-powered vehicles. Research waned from 1920 until the early 1960s when environmental issues of pollution and the fear of depleting natural resources created the need for a more environmentally friendly method of personal transportation.
EV Charging design
Today’s EVs are very different from ICE (internal combustion engine) gasoline-powered vehicles. The new breed of EVs has benefited from a series of failed attempts to design and build electric vehicles using traditional methods of production used by manufacturers for decades.
There are numerous differences in how EVs are manufactured when compared to ICE vehicles. The focus used to be on protecting the engine, but this focus has now shifted to protecting the batteries in manufacturing an EV. Automotive designers and engineers are completely rethinking the design of EVs, as well as creating new production and assembly methods to build them. They are now designing an EV from the ground up with heavy consideration to aerodynamics, weight and other energy efficiencies.
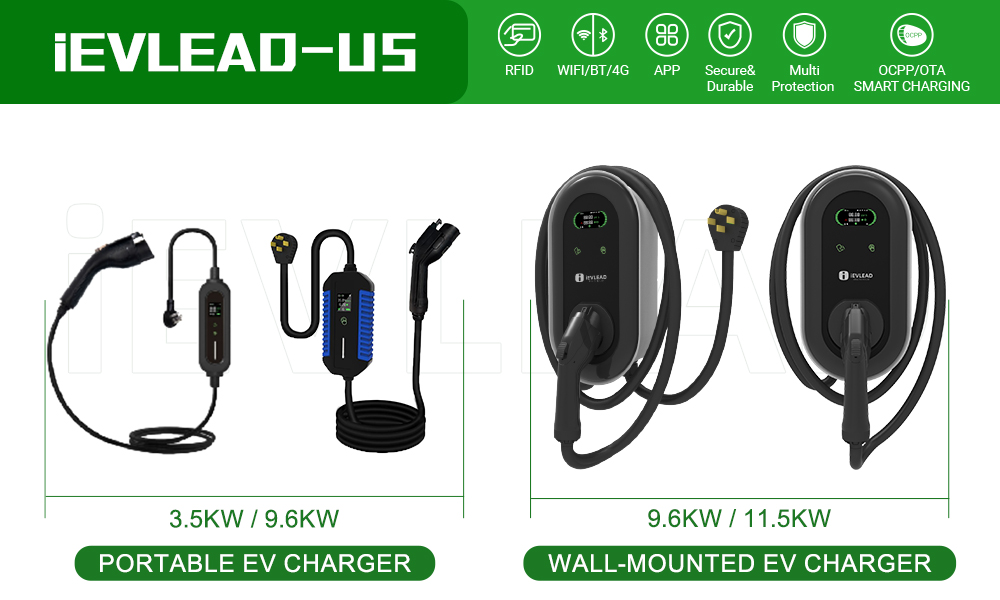
An electric vehicle battery (EVB) is the standard designation for batteries used to power electric motors of all types of EVs. In most cases, these are rechargeable lithium-ion batteries that are specifically designed for a high ampere-hour (or kilowatthour) capacity. Rechargeable batteries of lithiumion technology are plastic housings that contain metal anodes and cathodes. Lithium-ion batteries use polymer electrolyte instead of a liquid electrolyte. High conductivity semisolid (gel) polymers form this electrolyte.
Lithium-ion EV batteries are deep-cycle batteries designed to give power over sustained periods of time. Smaller and lighter, the lithium-ion batteries are desirable because they reduce the weight of the vehicle and therefore improve its performance.
These batteries provide higher specific energy than other lithium battery types. They are typically used in applications where weight is a critical feature, such as mobile devices, radio-controlled aircraft and, now, EVs. A typical lithium-ion battery can store 150 watt-hours of electricity in a battery weighing approximately 1 kilogram.
In the last two decades advances in lithium-ion battery technology has been driven by demands from portable electronics, laptop computers, mobile phones, power tools and more. The EV industry has reaped the benefits of these advances both in performance and energy density. Unlike other battery chemistries, lithium-ion batteries can be discharged and recharged daily and at any level of charge.
There are technologies that support the creation of other types of lighter weight, reliable, cost effective batteries — and research continues to reduce the number of batteries needed for today’s EVs. Batteries that store energy and power the electric motors have evolved into a technology of their own and are changing almost every day.
Traction system
EVs have electric motors, also referred to as the traction or propulsion system — and have metal and plastic parts that never need lubrication. The system converts electrical energy from the battery and transmits it to the drive train.
EVs can be designed with two-wheel or all-wheel propulsion, using either two or four electric motors respectively. Both direct current (DC) and alternating current (AC) motors are being used in these traction or propulsion systems for EVs. AC motors are currently more popular, because they do not use brushes and require less maintenance.
EV controller
EV motors also include a sophisticated electronics controller. This controller houses the electronics package that operates between the batteries and the electric motor to control the vehicle speed and acceleration, much like a carburetor does in a gasoline-powered vehicle. These on-board computer systems not only start the car, but also operates doors, windows, air conditioning, tire-pressure monitoring system, entertainment system, and many other features common to all cars.
EV brakes
Any type of brake can be used on EVs, but regenerative braking systems are preferred in electric vehicles. Regenerative braking is a process by which the motor is used as a generator to recharge the batteries when the vehicle is slowing down. These braking systems recapture some of the energy lost during braking and channel it back to the battery system.
During regenerative braking, some of the kinetic energy normally absorbed by the brakes and turned into heat is converted to electricity by the controller — and is used to re-charge the batteries. Regenerative braking not only increases the range of an electric vehicle by 5 to 10%, but it also has proven to decrease brake wear and reduce maintenance cost.
EV chargers
Two types of chargers are needed. A full-size charger for installation in a garage is needed to recharge EVs overnight, as well as a portable recharger. Portable chargers are quickly becoming standard equipment from many manufacturers. These chargers are kept in the trunk so the EVs’ batteries can be partially or completely recharged during a long trip or in an emergency like a power outage. In a future issue we will further detail the types of EV charging stations such as Level 1, Level 2 and Wireless.
Post time: Feb-20-2024